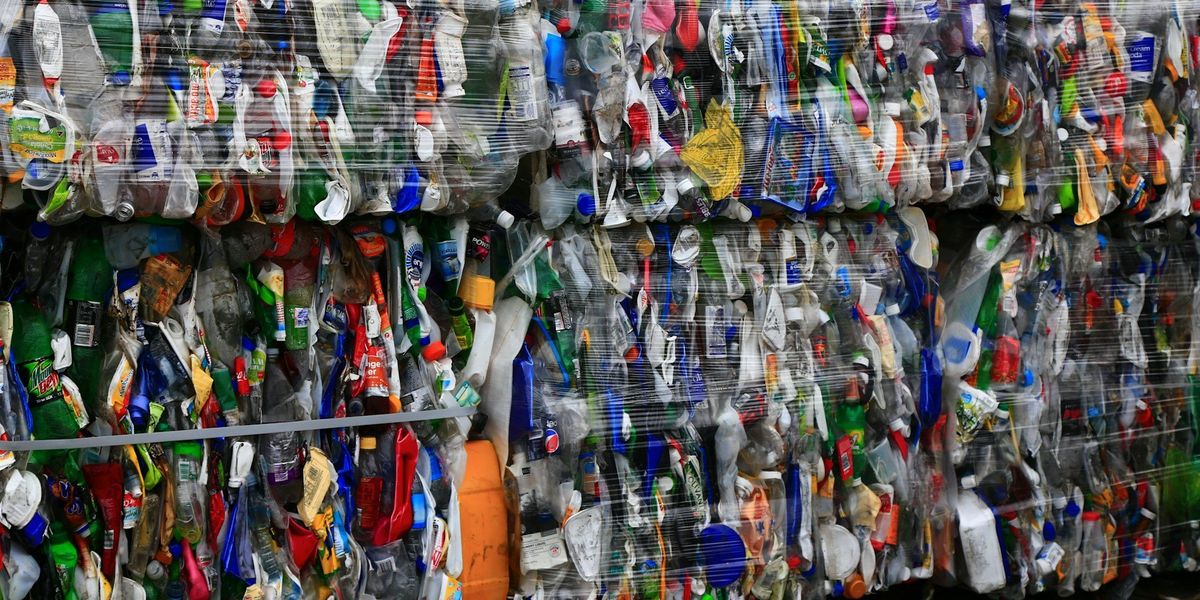
Another chemical recycling plant closure offers ‘flashing red light’ to nascent industry
Fulcrum BioFuels’ shuttered “sustainable aviation fuel” plant is the latest facility to run into technical and financial challenges.
For the second time this year, a chemical recycling plant built to turn waste into usable products has closed, casting further doubt on the viability of an upstart industry that has been plagued by financial and technical challenges in its effort to scale up.
Fulcrum BioFuels launched its Sierra plant outside Reno, Nevada, in 2022 with the goal of converting municipal solid waste into “sustainable aviation fuel.” But in May of this year the company suddenly laid off its roughly 100 employees and shuttered its website, as Bloomberg first reported. The decision came just as the plant was ready to reopen after a series of technical challenges had forced it offline, continuing a trend of delays and setbacks for a facility that had initially been slated to open in 2010.
Fulcrum representatives did not respond to emails and phone calls and little is yet clear about the company’s future, while its plans to build a larger plant in Gary, Indiana, appear to be hanging on by a thread following bond defaults. Carolyn McCrady, a co-founder of Gary Advocates for Responsible Development, which formed in 2021 to oppose Fulcrum’s plans, said her organization is still challenging Fulcrum’s air permit to build a plant in the city as it waits to learn more about the company’s next steps.
“We feel vindicated and that we were right all along,” McCrady told EHN. “We think all communities should put on their critical thinking hats when people like these come to town and offer something that’s too good to be true.”
As of September 2023, there were 11 constructed chemical recycling facilities in the country using pyrolysis or gasification to convert plastic into fuel or chemicals that can then be used to create new plastic, according to a report from Beyond Plastics and the International Pollutants Elimination Network. Two of those have now closed — news welcomed by environmental advocates concerned that the plants encourage plastic production and discourage solutions that address the roots of the global plastics crisis. Greenhouse gas emissions from the processing of plastic waste are also 10 to 100 times worse than those from the production of virgin plastic, and the release of plastic additives during chemical recycling can cause reproductive, cardiovascular and endocrine harm, the Beyond Plastics report found.
For the chemical recycling industry—facing a precarious moment with state legislation and a global plastic treaty developing—the closure is another indication of financial, technical and regulatory headwinds. Last fall, Youngstown City Council in Ohio voted against SOBE Thermal’s proposal for a plant that would have converted tires into gas. In February, the Regenyx plant in Oregon, which converted plastic waste into a polystyrene precursor, closed before ever reaching capacity, suffering millions in financial losses in the process. And in April, Encina canceled its plans to build one of the country’s largest chemical recycling plants in Pennsylvania.
The chemical recycling industry “will continue to face enormous challenges, both in securing financing, operating economically and producing products that companies want to buy,” Jenny Gitliz, director of solutions to plastic pollution at Beyond Plastics, told EHN. The fact that plastic has so many different chemicals in it further complicates the various conversion processes now in use, Gitliz explained.
Closure a “black eye” for waste-to-fuel efforts
Fulcrum launched in Pleasanton, California, in 2007, focused on developing the infrastructure to use an unusual feedstock to create jet fuel: municipal solid waste. At its Sierra plant, it turned shredded waste, including up to 20% plastic, into synthetic gas through a process called gasification, which heats the feedstock in a low-oxygen environment. After a second step in which the gas is cleaned up, it enters a Fischer-Tropsch reactor, in which it is converted into aviation fuel. Fulcrum’s facility was the first to license the Fischer-Tropsch technology, designed by BP and Johnson Matthey. A spokesperson for BP declined to comment on the closure of Fulcrum’s plant but said the technology can operate economically at large and small scales and is “a key technology in e-fuels production pathways” that it plans to continue to license and commercialize.
The chemical recycling industry “will continue to face enormous challenges, both in securing financing, operating economically and producing products that companies want to buy.” — Jenny Gitliz, director of solutions to plastic pollution at Beyond Plastics
The Sierra plant cost $300 million to build and had a capacity of 12 million gallons of sustainable aviation fuel, or SAF, per year, according to a report published last fall by Beyond Plastics and IPEN. But its first shipment contained just 350 gallons, Bloomberg reported, and the unexpected creation of nitric acid, emissions of nitrogen oxide and the buildup of material in its gasification process contributed to a start-and-stop nature that prevented the plant from ever reaching capacity.
Before closing the Sierra plant, Fulcrum had entered forbearance on $289 million in bonds. The Indiana Finance Authority had authorized $500 million in bonds for Fulcrum’s planned facility in Gary, but the company failed to secure funding for the 52-acre lakefront property where it hoped to build, McCrady said, delaying that project. Fulcrum had also announced its intention to build facilities in Baytown, Texas, and the United Kingdom.
Fulcrum’s partners on the Sierra project included Waste Connections, which was slated to supply waste to the facility and did not respond to a request for comment on the closure. United Airlines invested $30 million in Fulcrum and did not respond to a request for comment. Fulcrum also had an offtake agreement with Japan Airlines, which did not respond to a request for comment. BP had invested $30 million in Fulcrum with a plan to take up to 50 million gallons of fuel per year from its plants, far exceeding the Sierra plant’s capacity.
The aviation industry is racing to meet its goal of making 10% of its fuel sustainable by 2030, but the total SAF volume of 160 million gallons in 2023 was “a drop in the bucket” of the total 100 billion gallons of fuel used, said Steve Csonka, executive director of the Commercial Aviation Alternative Fuels Initiative, a public-private partnership formed in 2006. The conversion of municipal solid waste into fuel could still contribute to that effort—as could the Sierra plant if it’s brought back online by another company—despite the challenge of utilizing a non-homogenous feedstock, Csonka said. But the Sierra plant’s closure is a “black eye” that will hinder that broader project, he said.
Chemical recycling controversy
Ross Eisenberg, president of America’s Plastic Makers, an industry trade group, said in a statement that 10 new or expanded chemical recycling facilities are in development and the industry is in the midst of a normal, lengthy process to scale up. “With chemical recycling able to produce a wide variety of products at the same time as hundreds of companies are committing to use more recycled plastic, there is a tremendous opportunity in the U.S. to recycle more of our post-use materials,” he said.
But to Anja Brandon, associate director of U.S. plastics policy at the Ocean Conservancy, the Sierra plant’s closure is further evidence that the environmental impacts and economics of chemical recycling “just don’t add up.”
“It’s a flashing red light for these other facilities—really for the potential investors or lenders to these other facilities—that this is an industry that has and continues to fail, which I hope decreases the investment and drive for these types of facilities and opens up the market for investments in real upstream solutions,” Brandon told EHN.